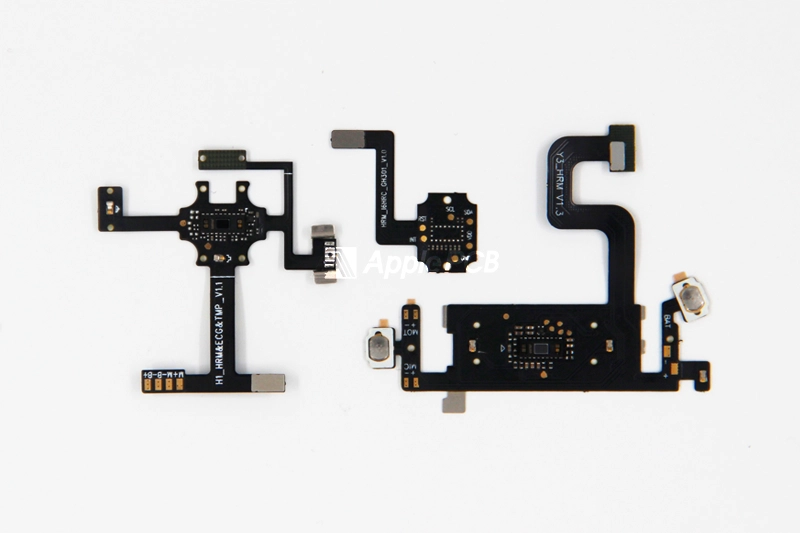
In the field of medical equipment, PCB, as the carrier of electronic components, is the core component to ensure the safety and reliability of the equipment. There are significant differences between medical PCBs and ordinary PCBs in the three aspects of material selection, design layout, and compliance, which are directly related to the long-term stability of medical devices. In this article, we will analyze the differences between the two to help you better understand the unique value of medical PCBs.
Differences in Material Selection for Medical PCB
Compared with ordinary PCBs, medical PCBs have strict requirements in terms of materials. Medical PCBs must comply with RoHS (Restriction of Hazardous Substances) standards, which prohibit the use of hazardous substances and ensure that the devices are safe for patients.
Under this premise, medical PCBs have a variety of materials to choose from. If the medical device often operates in a high temperature environment, high Tg, metal substrate, Teflon or ceramic materials can be used, which can enhance the heat dissipation ability of the medical PCB. If there is a need for portable and bendable applications then polymer materials such as polyimide can be chosen.
In addition, due to the high demand for failure analysis and quality control in medical devices, the selection of medical PCB materials requires strict process documentation and product traceability (some large medical terminals require 10 years of process record traceability). This helps in effective tracking and rectification in case of problems.
Differences in the Design of Medical PCB
1.Flexible Design
In addition to HDI design, flexible PCBs are also popular in the medical industry. This is because medical devices such as ultrasound probes, wearables and implantable instruments often require non-standard dimensions and complex structures. Medical flexible PCBs can bend and fold to accommodate complex 3D structures by using polyimide substrates, which is difficult to achieve with ordinary PCBs.
2.High Accuracy Signal Transmission
Medical devices require extremely high accuracy in signal transmission. For example, devices such as ECG machines and ultrasound machines need to accurately capture and transmit weak bioelectric signals. Therefore, medical PCBs are mostly designed to ensure signal integrity and avoid signal attenuation, reflection or crosstalk.
- Multilayer PCB design: Medical PCBs often use multilayer PCBstructures to reduce interference through separate signal and power layers.
- Impedance control: High-frequency signal transmission requires precise impedance matching, which is usually achieved through strict wiring rules and material selection.
3.High Density Design
Medical devices often need to integrate more functions in a limited space, so there are many medical HDI PCBs. compared with ordinary PCBs, medical HDI PCBs achieve higher integration and smaller size by increasing the number of layers and reducing the spacing between components.
Differences in the Compliance of Medical PCB
The compliance requirements for medical PCBs are much higher than ordinary PCBs, and the core differences are reflected in three aspects:
1.ISO 13485
The ISO 13485 standard is the international standard that medical PCBs generally follow. It ensures that PCB manufacturers have established a comprehensive quality management system covering the entire process of design, development, production, installation and service. Choosing a manufacturer that has passed the ISO 13485 standardized system can greatly reduce the potential risks and quality problems of medical PCBs.
2.IEC 60601
IEC 60601 is an international standard applicable to medical electrical equipment. It ensures that medical PCBs are electrically safe, electromagnetically compatible and environmentally adaptable to prevent electric shocks and other electrical hazards.
3.UL 60601
UL 60601 is the U.S. safety standard for medical electrical equipment, similar to IEC 60601 but applicable to the U.S. market. For medical PCB manufacturers, ensuring that PCBs comply with UL 60601 is a requirement for entry into the U.S. market.
4.RoHS
RoHS certification is the European Union's environmental protection regulation for electronic and electrical equipment. The directive restricts the use of hazardous substances such as lead, mercury, cadmium, and hexavalent chromium in medical devices and PCBs. Medical PCBs must comply with the RoHS directive to ensure that they do not pose a risk to human health.
5.FDA Regulations
The U.S. Food and Drug Administration (FDA) is one of the major regulatory agencies in the U.S. for medical devices. Through its Center for Devices and Radiological Health (CDRH), the agency is responsible for overseeing medical devices that emit radiation and evaluating the potential risks they may pose to those around them. In addition, the FDA categorizes medical devices based on the level of risk they pose to patients and operators.
Differences in the Applications of Medical PCB
Unlike ordinary PCBs, medical PCBs are very specialized in Applications and functions. The requirements for PCBs in different segments are also very different, and ApplePCB is committed to providing targeted solutions.
Blood Glucose Monitoring Device
- Application: Daily health management device for diabetic patients
- Core requirements: ultra-small size, more than 10 years of service life, millivolt signal accuracy
- Recommended solution: Flexible PCB, HDI PCB, rigid-flex PCB
Wireless Blood Pressure Monitor
- Application: Portable blood pressure monitoring device supporting Bluetooth/Wi-Fi connectivity
- Core requirements: anti-motion interference, compact design, low power consumption
- Recommended solution: Flexible PCB, Multilayer PCB
Medical Gas Management Equipment
- Application: Real-time monitoring of medical gas concentration and volume
- Core requirements: corrosion resistance, sealing, high reliability
- Recommended solutions: Flexible PCBs, Multilayer PCBs
Medical Imaging Equipment (MRI)
- Application: magnetic resonance imaging system
- Core requirements: high-speed signal transmission, signal integrity, anti-electromagnetic interference
- Recommended solutions: HDI PCBs, RF/microwave PCBs, High-speed digital PCBs
Nurse Call and Alarm System
- Application: Hospital Nurse Call and Emergency Alarm Equipment
- Core requirement: 7×24 hours stable operation, long life time
- Recommended solution: Flexible PCBs, Multilayer PCBs
Ophthalmic Diagnostic Equipment
- Application: Ophthalmic surgery and diagnostic equipment
- Core requirements: micron-level laser control precision, anti-static design
- Recommended solution: Flexible PCBs, Multilayer PCBs
Oxygen Analysis and Distribution Equipment
- Application: Oxygen concentration monitoring and delivery system
- Core requirements: zero-failure operation, high reliability
- Recommended solutions: Flexible PCBs, Multilayer PCBs
Sensor Devices
- Application: gas analyzer, blood tester, ultrasonic equipment, endoscope, ECG, etc.
- Core requirements: miniaturized design, long service life
- Recommended solutions: HDI PCB, Multilayer PCBs, Flexible PCBs
Wearable Medical Devices
- Application: Health tracking devices (e.g. heart rate monitoring, blood oxygen detection)
- Core requirements: ultra-thin design, waterproof and bend-resistant
- Recommended solution: HDI PCB, Multilayer PCB, Flexible PCB, Rigid-flex PCB
Wrapping Up
Every medical PCB carries an uncompromising responsibility. ApplePCB has been deeply engaged in the medical electronics field for 15 years, and serves the global medical equipment with professional ability.
- Authoritative certification: certified by ISO 13485, IEC 60601, FDA and other global medical standards.
- Experience: Cumulatively provided high-reliability PCB solutions for 200+ medical device manufacturers.
- Global service: customers cover 20+ countries and regions in North America, Europe, Asia, etc.
If you have medical PCB design or manufacturing needs, please feel free to contact our expert team for customized solutions!