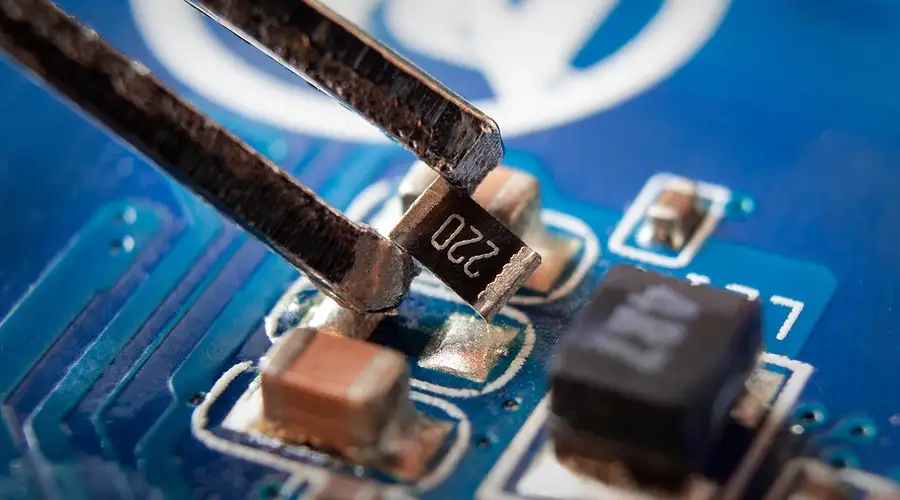
Surface mount devices, also known as SMDs are parts that are directly connected to the surface of a printed circuit board (PCB). This innovative mounting method, called surface mount technology (SMT) has transformed the development of electronics manufacturing. Its efficiency and accuracy have established it as the approach for creating modern electronic devices.
Although SMT predominantly uses surface mount components it can incorporate through hole technology (THT) components when needed. Nevertheless the majority of components, in SMT are SMDs providing benefits in terms of size reduction, performance enhancement and automated assembly processes.
What is a Surface Mount Device (SMD)?
SMD, or Surface Mount Device, refers to a specific type of electronic component. Unlike older components that required insertion through drilled holes, SMDs are directly mounted onto the surface of a PCB. This eliminates the need for drilling, leading to a more efficient assembly process and enabling the creation of smaller, lighter, and more densely packed electronics.
The rise of miniaturized electronics has spurred significant advancements in circuit board manufacturing. One prominent example is the widespread adoption of SMT, which has largely supplanted the older THT in applications demanding compact or slim designs. Unlike THT, where components are inserted through pre-drilled holes, SMT involves directly soldering components onto designated pads on the board's surface.
Characteristics of SMD
SMD technology is characterized by its distinct shape and structure, differing from traditional through-hole components. These devices are notable for their small size, lightweight, and minimal or absent leads, enhancing their reliability. They are also designed to withstand shock, vibration, and interference, making them robust in various operating conditions. The adaptability of SMDs for semi-automatic and automatic assembly processes is facilitated by their packaging in tape and reel, tube, or tray formats, which streamlines assembly efficiency and is conducive to high-density circuit design.
The employment of SMD technology not only minimizes the solder joint failure rate—less than ten parts per million—but also allows for a significant increase in the operating frequency of electronic circuits, reaching up to 3000MHz, compared to 500MHz for through-hole components. This advancement contributes to a reduction in parasitic parameters, thus enhancing the high-frequency characteristics and operational speed of the equipment. Additionally, SMD products are recognized for their high dimensional accuracy and consistency, which further underscores their quality and reliability in electronic assemblies.
Disadvantages of SMD
SMDs necessitate specialized manufacturing techniques and equipment due to their higher complexity, presenting unique challenges in their assembly and integration. Repairing or replacing individual SMDs can be difficult, requiring specific tools and expertise, which underscores the need for careful handling. Their small size makes them particularly sensitive to mishandling or electrostatic discharge (ESD), posing additional risks during handling and integration. Furthermore, some SMDs may face limitations in high-power applications, as their compact dimensions and thermal capabilities restrict their power handling capacity, necessitating careful consideration in the design and application of SMD-based circuits.
The Major Differences Between SMD and SMT
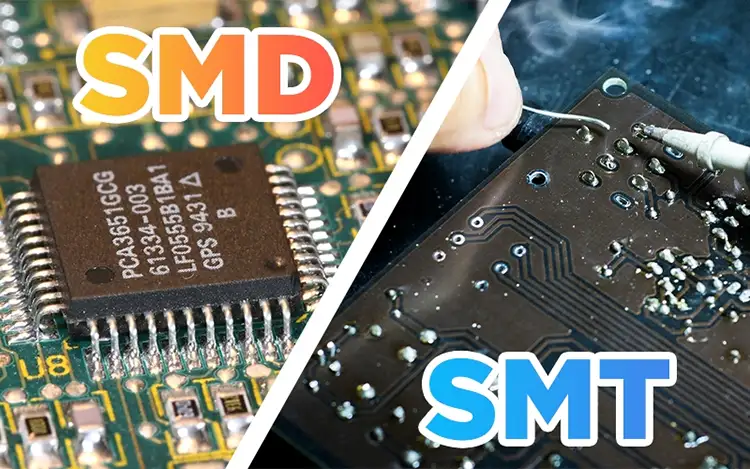
A SMD is a type of electronic device that is mounted directly onto the surface of a PCB.
SMT refers to the method employed to produce an SMD. This technology has largely supplanted the traditional through-hole method, which involves inserting component wires into the circuit board's holes.
While SMT is predominant, through-hole technology is still utilized for certain components like large transformers and power semiconductors requiring heat sinks, allowing both methods to coexist on a single PCB.
SMT components tend to be smaller than their through-hole counterparts, attributed to their reduced lead size or the absence of leads. These components might feature short pins, various styles of leads, flat contacts, a grid of solder balls (for ball grid arrays or BGAs), or terminations situated on the component’s body.
Why Companies Choose to Combine SMD and SMT Technologies?
Early SMDs presented a challenge: their small size and intricate designs required manual placement and soldering. While machines could handle some of the workload, their capabilities were limited in terms of component types and sizes.
With the advent of SMT, the assembly process has become faster and more accurate. In the past, attaching a component to a circuit board involved manually positioning small fragments of silver or lead. Nowadays, solder paste, a blend of flux and tiny solder particles, is still utilized for this purpose. In contrast to manual labor, where an individual might manage to attach a few hundred SMDs per hour, SMT equipment can handle thousands. Consequently, for almost every traditional through-hole method, there is now a corresponding SMT process.
The efficiency and cost-effectiveness of SMT in producing circuit boards rapidly contributed to the proliferation of surface-mount devices. This development has led to the optimization of both time and board space, with SMDs enabling denser and more accurate assemblies.
Furthermore, SMT has facilitated swifter and more precise construction processes. The shift towards SMDs in SMT platforms by electronics manufacturers is increasingly evident, driven by the significant savings in both time and costs.