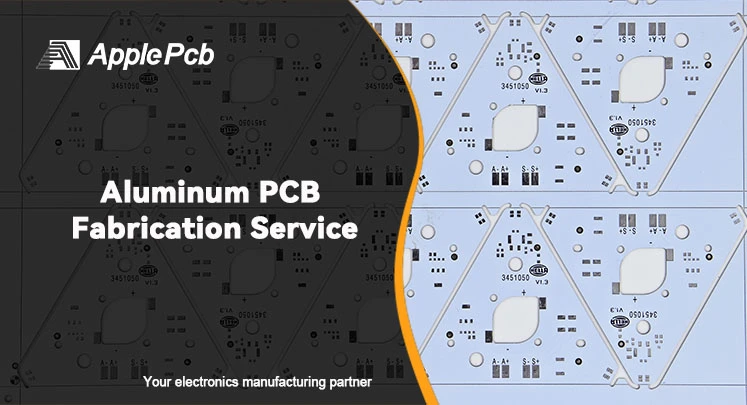
The production of aluminum PCB has risen significantly as the need for heat dissipation in device continues to increase. In this article, we will take an in-depth look at the characteristic, structure, and different types of aluminum printed circuit boards. In addition, as experts in aluminum PCB manufacturing, we will also discuss the challenge and solution faced in the production of aluminum PCB and provide you with a professional guide to selecting material of aluminum PCB.
Why Are Aluminum PCBs Widely Used in the Industry?
When it comes to metal core PCB (MC PCB), the first thing that comes to mind is aluminum PCB, it's also known as aluminum base PCB, aluminum clad PCB, aluminum core PCB and aluminium leiterplatten. It is not difficult to observe our entire electric industry, aluminum PCB is the most used MC PCB, So what makes aluminum PCBs stand out?
Traditional PCBs are usually made of FR-4 or CEM1-3 materials, which have low cost and excellent overall performance, but are not very good at heat management. In cases where the requirements for heat dissipation are not very high, we can use thermal vias or heat sinks to assist in heat dissipation, but when it comes to high power components that need to generate more heat, traditional heat dissipation methods are not good enough to meet their heat dissipation needs. This is because it often leads to expensive costs and bulky products.
In this case, the excellent thermal conductivity of metal core PCBs (MC PCBs) comes into play. Currently metal core are Iron, copper and aluminum. They each have their own characteristics and applicable scenarios, and their differences are described in detail below.
Iron PCB
Iron PCBs offer improved stability and electromagnetic shielding along with a low coefficient of thermal expansion (1.17×10-3) making them particularly well suited for ceramic lamps. However their thermal conductivity coefficient falls short compared to other MC PCBs and the hardness of iron presents challenges in the manufacturing process. Therefore, although the iron itself is not costly, the overall cost can be higher due to the complexity of manufacturing.
Copper PCB
Copper PCB has the best mechanical strength, durability, and thermal conductivity (twice that of aluminum PCB), so they are widely used in high-power rectifiers, overload relays, solar power converters, renewable energy equipment, railroad systems, and monitor power cords, etc. However copper PCB are also the most expensive of the three, so if your application doesn't require much in the way of thermal conductivity, etc, then consider aluminum PCB as a more economical option.
Aluminum PCB
Aluminum PCBs have a high thermal conductivity of about 200 W/MK, which can satisfy most applications that require good heat dissipation. In addition, aluminum is cheaper than copper, softer than iron, and easier to process and form. Therefore, its material and manufacturing costs are relatively moderate. Aluminum PCBs are widely used and can be found in LED, power supply, communication electronic, automobile, power module, audio, and other equipment.
So Aluminum PCB board became the MC PCB for engineers and manufacturers as first choice, balancing thermal conductivity, processability, and cost.
Advantages and Disadvantages of Aluminum PCB
Aluminum printed circuit board are widely used in application however they may not be ideal for every scenario. Let's discuss the advantage and disadvantage to help you decide if aluminum PCB is the choice for your product solution.
Advantages of Aluminum PCBs
● Heat dissipation: Aluminum PCB has excellent heat dissipation properties, it is only one-tenth the thickness of traditional FR-4, but its dielectric can be 5-10 times more thermally conductive, meaning that it has an extremely high thermal management efficiency, which allows it to quickly dissipate heat generated by electronic component to avoid overheating and damage problem.
● Environmentally friendly: Aluminum is an eco friendly material that can be recycled making it compliant with RoHS regulations. So if your brand pursues environmental friendliness and wants to enhance the green phenomenon of your company, then aluminum PCB will be a good choice.
● Lightweight: Aluminum is lighter than copper and stainless steel, which helps shed the weight of the entire device. In some weight-sensitive area such as aerospace and mobile device, aluminum substrate PCBs can meet their lightweight needs.
Disadvantages of Aluminum PCB
● Increase in Cost: Aluminum as a metal, its material cost is higher than traditional materials such as epoxy resin, in addition to the treatment of the metal substrate also requires a more delicate manufacturing process and another advanced equipment. Therefore, your initial investment in aluminum PCB fabrication may be higher.
● Processing complexity:Soldering and routing aluminum PCBs can be tricky requiring sophisticated processes and advanced equipment that push aluminum PCB manufacturer to up their game.
● Limited application: Aluminum PCB are mainly used for high-power electronic device that requires high heat dissipation function. For low-power or applications that do not require high heat dissipation, traditional FR-4 PCB may be more economical.
The Structure of Aluminum PCB
The structure of an aluminum PCB closely resembles that of a FR 4 PCB. Both types feature layers of copper foil, a dielectric layer, and a substrate layer. The key variation lies in the material used for the substrate, in the aluminum PCB, which is aluminum metal. Plus, it along with a layer of aluminum base film. Most aluminum PCBs consist of 1-2 layers and the structure is relatively simple. However, some high-power applications may require more complex structures, and ApplePCB can produce aluminum PCBs with up to 6 layers.
1.Copper Foil Layer: The layer of copper foil, on an aluminum circuit board is quite thick typically ranging from 1 to 10 ounces, is positioned at the top of the board. This thicker copper layer offers increased capacity for carrying current.
2.Dielectric layer: Also known as the thermal insulation layer, this layer is the core of the aluminum printed circuit board, located in the middle of the copper layer and the aluminum base layer, with thermal conductivity, insulation, and bonding. It is the largest insulation layer in the power module structure. Depending on the application we can choose different material as dielectric layer.
3.Aluminum base layer: The aluminum base layer consists of an aluminum substrate, typically white. It offers excellent thermal conductivity, efficiently dispersing heat to surrounding areas to keep electronic devices within safe temperature limit. Moreover, it provide mechanical support for the aluminum printed circuit board.
4.Aluminum base membrane layer: The layer of aluminum provide protection by safeguarding the aluminum surface from scratch and undesired etching. Usually the thickness of the aluminum base film layer is 1 mm.
Material Selection Guide for Aluminum PCBs
Once we grasp the layout of Aluminum PCB we'll offer a guide on selecting materials. This guide aim to assist you in making an informed material choice based on the structure layers.
1. Selection of Aluminum Substrate
According to the material of the aluminum substrate, the most common are aluminum alloy 5052 and 6061. 5052 is aluminum-magnesium alloy, and 6061 is aluminum-magnesium-silicon alloy. In comparison, 6061 has better overall function but is also more expensive. Below is a comparison of the thermal property of the two alloys:
Thermal Properties | Aluminum5052 | Aluminum6061 |
Melting Point Range (℃) | 605/650 | 582/652 |
Linear Expansion10-6k-1(20-100℃) | 23.8 | 23.6 |
Specific Heat Capacity J/kg-K(0/100℃) | 900 | 896 |
Heat Conductivity W/m-k(20℃) | 138 | 167 |
Aluminum-based PCBs are usually used in high-power products, so heat dissipation is the primary consideration, ApplePCB provides aluminum substrates from well-known and reliable brands and comes with test reports from authoritative institutions to ensure the accuracy of the thermal conductivity. Below are the models of aluminum substrates we provide and their thermal conductivity coefficients:
Brand Model | Thermal Conductivity |
BOYU AL-01-B10 | 1W/M.K |
BOYU AL-01-B20 | 2W/M.K |
BOYU AL-01-B30 | 3W/M.K |
TCB-4 | 4W/M.K |
JQ133 | 2W/M.K |
JQG05 | 5W/M.K |
Generally speaking, thermal conductivity of 1.0-1.5W/m-k belongs to low thermal conductivity aluminum substrate, and thermal conductivity of 1.5-3.0W/m-k belongs to medium thermal conductivity aluminum substrate. In this range we can choose the BOYU series and JQ133, they are very suitable for applications that require low to medium thermal performance, such as low power led aluminum PCB and small electronic devices.
The thermal conductivity above 3.0W/m-k belongs to a high thermal conductivity aluminum substrate PCB. If you need to apply aluminum PCBs to high-power products, such as power modules and high-power LEDs, then ApplePCB suggests that you choose TCB-4 and JQG05 because they have higher thermal conductivity.
2. Selection of Dielectric Material
ApplePCB can provide epoxy glass fiber prepreg, epoxy resin, polyimide, glass fiber prepreg, and polyolefin resin, five types of dielectric layer materials. Depending on the specific application, you can choose different materials.
Generally, we will use epoxy glass fiber prepreg as the dielectric layer material, it has good mechanical strength and electrical properties, suitable for general aluminum PCB, if you need high thermal conductivity aluminum PCB, then you should choose high thermal conductivity epoxy resin. If you need to make High-Frequency PCB, then you can choose polyimide or polyolefin resin glass fiber prepreg, both have low dielectric constant and low loss factor, which can perform well in High-Frequency environments.
In addition the thickness of the dielectric material should also be considered, because if the dielectric layer is too thick, it will affect the thermal conductivity; if it is too thin, although the heat dissipation effect is better, but it is easy to cause short circuits between the metal core and the wire. Therefore, you need to select the appropriate thickness of the dielectric layer according to the specific application of the thermal requirements. ApplePCB can provide four different dielectric thickness options: 0.1mm/0.12mm/0.15mm/0.2mm, can cover your different application requirements.
If you are still not sure which specification is suitable for your application, you can contact us in the lower right corner, ApplePCB's experienced technicians will provide you with reference suggestions to help you choose the most suitable aluminum Laminate material.
3. Selection of Copper Cladding
ED copper foils will suffice for general applications, but if you need thicker copper foils and high flexibility, calendered copper foils will work better. The thickness of the copper foil should be chosen according to the current demand of the specific application, low power applications can choose 0.5oz or 1oz copper foil, while high power applications are best to choose 2oz or 3oz copper foil.
ApplePCB can provide four thicknesses of copper foil, Hoz, 1oz, 2oz, and 3oz, and the back side of our copper foil is uniformly oxidized chemically with zinc or brass plating to ensure that the copper foil is not damaged. zinc-plated or brass-plated to increase the peeling strength. This practice can effectively improve the bonding strength between the copper foil and the dielectric layer, and enhance the durability of the aluminum PCB.
4. Selection of Protective Film
When selecting a protective film, processing temperature is an important factor. For temperature below 120 degrees, PET protective film is a cost effective option. For higher temperature processes like tin spraying, ApplePCB recommend using PI protective film. The PI film can withstand temperature up to 250 degrees, providing effective protection for the aluminum substrate during high temperature operations above 120 degrees.
Different Types of Aluminum PCB
ApplePCB has a wealth of expertise, in producing kinds of aluminum PCBs.
1. Single Side Surface Mount Aluminum PCBs
This is the simplest and easiest aluminum PCB to manufacture and the lowest cost. Heat is transferred from the component to the wiring layer, through an intermediate insulating thermal conductive layer, and then to the aluminum base layer. It is mainly used for application such as LED lighting, audio equipment and power module.
2. Single Side Surface Mount Double Layer Aluminum PCBs
This type of aluminum PCB has two wiring layers and an insulating layer, are suitable for higher power application that require more complex circuit design, such as power management system. It requires the use of blind vias for signal paths or as thermal via, and therefore also requires a more precise machining process.
3. Double Sided SMT Dual Layer Aluminum PCBs
Double Side SMT Double Layer Aluminum PCBs are considered to be one of the more complex type of aluminum printed circuit board. This is because it involves wiring on both sides and through-hole design. From a manufacturing point of view it also increase the difficulty and cost of manufacturing because it involves complex procedure such as drilling through hole and thermal bonding.
4. General-purpose Aluminum PCB
It uses standard epoxy glass fiber prepreg as the dielectric layer, with better thermal performance, but not as good as the specialized high thermal conductivity aluminum PCB. Its cost is relatively low and suitable for the general thermal requirements of the application.
5. High Thermal Conductivity Aluminum PCB
The dielectric layer consists of epoxy resin (high thermal conductivity). Its cost is relatively high but it has excellent heat dissipation performance, which can conduct and emit heat quickly and significantly improve the heat dissipation efficiency of the equipment. Widely used in high-power PCB aluminium led lamps, industrial power modules, and other scenes that require efficient heat dissipation.
6. High Frequency Aluminum PCB
The dielectric layer consists of polyimide or polyolefin resin glass fiber prepreg so that it can maintain good electrical properties and stability under high-frequency conditions, so it is suitable for high-frequency communication equipment and microwave equipment. Its cost varies according to specific materials and design requirements. But generally speaking is higher than the high thermal conductivity of aluminum PCB.
7. Hybrid Aluminum PCB
Hybrid Aluminum PCB usually consists of two or four layers of FR-4 subassemblies. Manufacturers will bond these subassemblies to the aluminum PCB through thermal bonding. These structure provide better heat dissipation and mechanical stiffness.
These types may overlap, for example, ApplePCB can provide both High-Frequency and High Thermal Conductivity Aluminum PCB, so if you need to manufacture more complex Aluminum PCB then you can consider contacting us in advance and send us your Gerber information to speed up the project process.
8. Flexible Aluminum PCB
The flexible Aluminum PCB is made up of PI and ceramic filler along with aluminum allowing it to be bent into shape. This design helps in saving space for connector and cable although it come with a higher cost, for both design and production.
Challenges in Aluminum Base PCB Fabrication
While there are kinds of aluminum PCBs most encounter similar hurdles during manufacturing. Fortunately, ApplePCB has 15 years of experience in aluminum substrate manufacturing, with state-of-the-art production equipment such as German Burkle presses, Mitsubishi laser drilling machines, and Hitachi mechanical drilling machines, we can provide a customized solution for your needs.
1. Aluminum Surface
When producing aluminum PCBs it's crucial to prevent any scratches or contact with the aluminum base. This is important as any interaction with hands or chemicals may cause oxidation, discoloration and scuff marks on the surface. Therefore ensuring a manufacturing process without contaminating the surface poses a challenge in production.
How did ApplePCB solve it?
ApplePCB will apply a film or passivation process before the hot air leveling (HASL) process to provide additional protection, for the aluminum substrate aiming to prevent scratching and discoloration.
2. Copper Etching
Due to the application of aluminum PCBs, in high power density gadgets thicker copper foils are necessary potentially resulting in lines post etching.
How did ApplePCB solve it?
To solve this problem, ApplePCB will accurately control the etching coefficient in the case of copper foil exceeding 3oz, and perform engineering line width compensation to prevent the alignment width from exceeding the tolerance range after etching.
3. Solder Mask Printing
Like the previous problem, difficulty with solder mask printing are caused by thicker copper foil. This is because after the image has been etched, the copper thickness on the alignment increases, resulting in a significant height difference between the alignment surface and the substrate. This situation causes the solder mask to have difficulty adhering firmly and affect the quality of the aluminum PCB.
How did ApplePCB solve it?
To avoid this situation, ApplePCB uses high-quality inks from TAIYO, a well-known Japanese brand, and adopt double printing technology through automated solder mask machine. In addition, to cope with more complicated situations, we have mastered the advanced resin filling technology as a backup solution to further ensure the stability and reliability of the solder mask.
4. Via and Outline
Unlike traditional FR-4 materials, aluminum as a metal requires extra care in drilling and shaping these mechanical manufacturing processes, or else burr problems will occur, affecting the electrical strength of the aluminum PCB. Also if your aluminum substrate is used for communication power applications, then it is necessary to perform a high-voltage test. If there are burrs on the edges of the holes and the aluminum base then this will potentially lead to high-voltage test fires, leaks, and failures.
How did ApplePCB solve it?
So to create neat edges and burr-free vias, ApplePCB uses specialized molds and milling cutters. For aluminum PCBs with large copper thicknesses, we adjust the hardness and speed of the drill according to the specific situation. Use a harder milling cutter and adjust the speed of the milling cutter to the speed suitable for the aluminum substrate (usually about two-thirds slower than the speed of the milling cutter for fiberglass boards) to ensure the quality of the thick copper drilled holes and edges. To address the issue of vias and outline, we have compiled ApplePCB specific manufacturing capabilities, you refer to the table below:
Drill hole | Outline | ||
Item | Parameter | Item | Parameter |
Hole Size for Machine Drill | 1.0-6.4mm | Minimum Routing Bit | 1.0mm |
Insulation Hole | 0.5-6.4mm | Outline Dimension Tolerance | Standard:±0.13mm |
Minimum:±0.10mm | |||
Space From NPTH to Copper | 0.20mm | Outline Location Tolerance | ±0.10mm |
Hole Location Tolerance | ±3mil | Minimum Space From Copper to Milling for Avoid Copper Exposed | 0.20mm |
NPTH Tolerance | ±2mil | Minimum Space From Copper to v-Cut for Avoid Copper Exposed | 0.4mm |
Countsink Depth Tolerance | ±0.20mm | V-CUT Angle (Tolerance) | 30°(±5°) |
Countsink Diameter Tolerance | ±0.20mm | PCB Thickness for V-CUT | 0.6-3.0mm |
Countsink Angle | 90° | Jump V-cut Safe Space: | 8mm(pcb thickness≤1.6mm) |
Quality Testing of Aluminum PCBs
ApplePCB will conduct different quality test to guarantee the dependability of each aluminum PCB manufactured.
1. Appearance Inspection
In the previous we mentioned the aluminum surface and aperture burrs manufacturing difficulties, so in the aluminum PCB production is complete, we will also carry out an appearance check, ApplePCB uses a combination of manual and instrumentation visual quality inspection. Ensure that the aluminum substrate has no burrs in the holes and edges, solder mask integrity, and no surface defects such as oxidation, contaminants, pits, scratches, and so on.
2. Heat Resistance Test
To verify the reliability of aluminum PCBs in high-temperature environments, we conduct heat resistance tests. The temperature range of the test is 288±5°C, and the duration is about 30 seconds. The judgment standard is that there is no burst board, hard separation, or solder mask peeling.
3. Board Warpage
Aluminum PCB flatness is also very important, ApplePCB will be tested in accordance with IPC-TM-650 standards, which can ensure that the board warpage is less than 0.5%.
4. High Voltage Test
Earlier we have also mentioned the need for high-voltage testing of power supply and communication products. We will also test according to the IPC-TM-650 standard, the test voltage is generally required between 1500V and 2500V, and the time is about 5 to 10 seconds. In specific cases it may be necessary to test up to 3000 V. Depending on the specific situation AC or DC can also be selected.
5. Thermal Performance Test
When it comes to aluminum substrates ensuring resistance and thermal conductivity is crucial. At ApplePCB we conduct testing of our aluminum substrates following the ASTM D5470 standard, which's a recognized American Material Testing Standard. We provide authoritative test reports, for all our products.
Why Trust ApplePCB as Your Aluminum PCB Manufacturer?
With 15 years of experience in aluminum PCB manufacturing, ApplePCB has accumulated a wealth of technical and process knowledge and is able to handle different manufacturing requirement such as blind buried via, heavy copper, and multilayers, providing customer with the best solution.
1. Superior Manufacturing Aluminum PCB Capabilities
Specifications | Aluminum PCB Capabilities |
Layer | 1-6 Layers |
Build Time | 1-4 Weeks |
Aluminum PCB Types | Single-sided, Double-sided, Multilayer Aluminum PCB |
Hybrid Aluminum PCB | |
Flexible Aluminum PCB | |
High Frequency Aluminum PCB | |
High Thermal Conductivity Aluminum PCB | |
Quality Level | IPC-A-600 Class 3/2 |
PCB Thickness | aluminum substrate 0.6-5.0mm |
Thickness Tolerance | ≤1.0mm: +/-0.10mm, |
>1.0mm:+/-10%. | |
Minimum Trace Width/Space | 35um(1OZ) :6/6mil |
70um(2OZ) :8/8mil | |
105um(3OZ):12/12mil | |
Copper Thickness | 1OZ to 8OZ (35μm to 280μm) |
Manufacturing Condition | Full-line operation; Production Machines And Equipment Specialized For Aluminum PCBs |
Surface Finish | ENIG, OSP, HASL, Immersion Silver, Immersion Gold |
Solder Mask Brand | KSM-S6189(green, black, yellow, red, blue, matte gree, matte black) |
Taiyo PSR-4000 WT03 (white) | |
Taiyo PSR-4000 LEW3 (white) | |
LB-1900W (white) | |
Certification | IATF 16949:2016 |
ISO 9001:2015 | |
ISO 14001:2015 | |
ISO 13485:2016 | |
UL |
2. Complete Production Process and Competitive Price
Unlike some distributors of PCB product, ApplePCB has an aluminum PCB factory. It is equipped with a complete production line, auto-production equipment, and advanced technology. We can complete all manufacturing processes independently, with the fastest delivery time of 1 week. This also allows us to effectively control production costs, offer competitive pricing, and provide additional discounts when orders reach certain quantities.
3. Professional team and excellent customer service
An experienced team of experts and efficient customer service are available throughout the production process. Including pre-production quotation, aluminum PCB prototype evaluation, communication of design details during production, and synchronization of production progress. Logistics and transportation tracking after production. No matter where you are, we can ensure smooth communication.