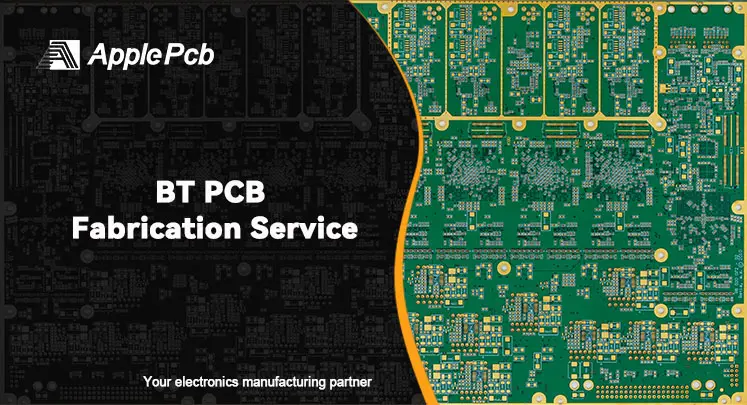
As the electronics industry demanded more robust and reliable components, research into advanced PCB materials intensified, drives the development of materials like BT resin. BT PCB's superior thermal and electrical properties made them ideal for applications in telecommunications, aerospace, and automotive industries. This article explores the advantages of BT PCBs and the reasons behind their effectiveness.
What Is BT PCB?
BT PCB stands for a type of printed circuit boards made with BT substrates as the foundation material. BT substrates consist of BT resin initially created by Mitsubishi Gas Chemical Co. in Japan. The BT resin is mainly made from the polymerization of Bismaleimide (B) and Triazine (T), leading to a thermoset resin with superior electrical, thermal and mechanical characteristics.
How Was BT PCB Invented?
1960s-1970s, the aerospace and defense industries, with their stringent requirements, drove the development of high-temperature resistant resins. Companies specializing in high-performance materials started to focus on developing resins like BT resin with even better properties.
BT resin is a key raw material for manufacturing BT substrates, initially developed by MGC in Japan in 1970s. Leveraging its significant technical expertise and first-mover advantage, even after the original patents have expired, the company has maintained a leading position in the global market for BT resin. Today, MGC accounts for over 90% of the global shipment volume of BT resin. Besides MGC, prominent manufacturers include Rogers, Isola, Nelco, Arlon, and Dow Chemical were involved in the development and refinement of BT resin.
What Is BT Resin?
BT resin stands for bismaleimide-triazine resin, is a top quality polymer used in making BT PCBs, it's a type of thermoset resin created by blending bismaleimide and triazine compounds.
Bismaleimide (BMI)
Bismaleimides are a type of imide compound known for containing maleimide groups, bismaleimide component enhances the resin thermal stability and mechanical performance leading to a high glass transition temperature (Tg). This feature enables the material to uphold its strength even under high temperatures.
Triazine
Triazines are a class of nitrogen-containing cyclic compound with three nitrogen atoms three carbon atoms. The triazine component enhances the resin thermal and chemical resistance. It also contributes to the low dielectric constant and low dissipation factor, crucial for high-frequency electrical performance.
Epoxy
Often blended with BMI to improve processability and reduce brittleness. Helps in achieving a balance between thermal performance and toughness.
Cyanate Ester
Sometimes added to enhance electrical properties and moisture resistance.
Flame Retardants
BT resin itself has triazine component contributing to its natural flame resistance. However, to meet stringent safety standards, additional flame retardants are often added. These include halogenated compounds, phosphorus-based retardants, inorganic compounds, and nitrogen-containing compounds.
Fillers
Inorganic additive like silica or alumina can be incorporated into BT substrates to enhance thermal conductivity and to modify coefficient of thermal expansion (CTE).
Glass Fibers
BT resin is usually strengthened with glass fiber, it is crucial for achieving the desired combination of mechanical, thermal and electrical properties. The particular kind and arrangement of glass fibers can be customized to meet the different applications.
Applications of BT PCB
BT PCBs are commonly employed in network chips and programmable logic devices like storage chips, mobile phone MEMS chips, communication chips, and memory chips, LED chips RF chips, and RF chips, BT PCB finds applications across industries such as consumer electronics, telecommunications, automotive electronics, computing and security equipment.
Advantages and Disadvantages of BT Resin PCB
The incorporation of BT resin into PCB production enhances the performance and reliability of BT PCB circuit boards. Its robust operation in harsh condition makes it ideal for critical component in industries like automotive, aerospace, telecommunications.
Advantages
Z-axis CTE below Tg | 55 ppm/℃ |
Z-axis CTE above Tg | 275 ppm/℃ |
Relative permittivity (Real Dk) | 3.70 @ 1 GHz |
Loss tangent | 0.015 |
Glass transition temperature | 180 ℃ |
Decomposition temperature | 325 ℃ |
Thermal conductivity | 0.35 W/m·K |
High Thermal Stability
Due to its high glass transition temperature (Tg) from 180 to 250°C, BT resin exhibits good thermal stability maintaining its structural integrity even under high temperature, it is ideal for applications where heat generation occurs.
Excellent Electrical Properties
BT resin offers low dielectric constant and loss tangent, making it ideal for the fabrication of high-performance multilayer BT PCB. This ensures signal integrity and minimizes signal attenuation in telecommunications, radar system, and high-speed computing.
Improved Dimensional Stability
BT resin exhibits low coefficient of thermal expansion (CTE), expands and contracts minimally with temperature changes. This is vital for precision electronics and aerospace components requiring dimensional stability and preventing issues like trace misalignment and solder joint failure.
Enhanced Moisture Resistance
BT resin's natural resistance to moisture absorption safeguards against dimensional changes and delamination, it is a good choice for applications exposed to humid condition.
Chemical Resistance
The inherent chemical resistance of BT resin equips BT PCB to withstand harsh operating environments involving acids and alkalis, it is suitable for applications exposed to chemicals or solvents.
Cost-Effective
While ceramic substrates are known for their excellent performance, but costs can be prohibitive. While BT circuit board cost is lower without compromising on essential performance characteristic.
Disadvantages
The inclusion of glass fiber layers in BT substrates increases their stiffness, this increased rigidity can pose challenges during the wiring and laser drilling processes, making it harder to achieve fine lines and precise hole.
Material Alternatives to BT PCBs
When selecting an alternative to BT substrates, to consider factors like thermal performance, mechanical properties, including rigidity, flexibility, and durability; and electrical properties, such as dielectric constant and signal integrity. Getting advice from ApplePCB can offer perspectives to assist you in finding the most appropriate alternative material to BT.
PTFE (Polytetrafluoroethylene)
Known for its excellent electrical properties especially at high frequencies, very low moisture absorption, and good chemical resistance. It's commonly used in RF and microwave applications. However, it falls short in mechanical strength and demands specialized processing techniques compared to alternative options.
Polyimide
Polyimide offers excellent thermal stability, withstanding temperatures up to 260°C. It's flexible allowing employed in dynamic or space constrained applications, and provides good dimensional stability. However, polyimide can be challenging to process and drill.
Ceramic Substrates
Ceramic substrates offer superior thermal conductivity, can withstand very high temperatures, and provide excellent dimensional stability. They fall short in much more expensive than organic substrate, brittle and prone to cracking, and heavier than polymer based alternatives.
Aluminum Substrates
For applications demanding high thermal conductivity such as LED lighting, power supplies, automotive electronics, aluminum substrates excel in thermal management, but may not offer the same level of electrical performance or suitability as other options, and they come with manufacturing challenges.
Liquid Crystal Polymer (LCP)
LCP can be manufactured into very thin, flexible substrates, it allows for the production of FPC that can be bent, folded, or shaped to fit application requiring flexible, dynamic circuits, such as wearable electronics, foldable devices, and high-frequency antennas.
Challenges in BT PCB Manufacturing
Manufacturing BT PCBs can be quite challenging when compared FR4. Overcoming these challenging calls for specialized equipment, processes, and knowledge. Partnering with ApplePCB can help navigate these difficulties and ensure a specialized equipment, processes, and expertise production of BT PCBs.
Material Handling
BT resin exhibits hard handling characteristic, such as brittleness, prone to cracking under mechanical stress.
Curing Process
Achieving optimal curing for BT resin is critical to ensure desired mechanical and electrical properties, the curing process needs precise temperature and pressure control.
Dimensional Control
Maintaining precise tolerance helps in minimizing signal loss, ensuring proper component fit, and maintaining the integrity of the electrical pathways, it involves precision manufacturing, such as advanced technique like laser drilling and high-precision CNC machining ensure accuracy.
Cost
BT PCBs are typically more expensive than standard FR4 PCB due to the higher cost of BT resin, offering superior performance characteristic such as high reliability and temperature resistance. The multilayer BT PCB cost is higher, contributes to the overall cost of BT PCB.
Availability
BT materials are more specialized than common FR4 materials, could lead to fewer suppliers and potentially longer lead time.
Check Our Capabilities
Feature | Capabilities |
Layer Count | 1-40L |
PCB Thickness | 0.2-8mm |
Thickness Tolerance | ≤1.0mm: +/-0.10mm, |
>1.0mm:+/-10%. | |
Minimum PCB Size | 2.5x2.5mm in panel, 10x10mm in single board. |
Maximum PCB Size | 500x1200mm |
Maximum Copper | 18oz |
Materials | MGS, Rogers, Isola, etc. |
Min Tracing/Spacing | 3mil/3mil |
Surface Finish | plating NI/AU, plating hard Gold, ENIG, Immersion Tin, Immersion silver, OSP, ENIG+OSP |
Impedance Control | ±10% |
Applications | Memory chip, RF chip, MEMS chip |
Drilling | Minimum mechanical drill diameter 0.15mm (6mil) |
Minimum laser drill diameter 0.075mm (3mil) | |
Min Annular Ring | 4mil |
Lead time | 4-7 business days |
Certification | UL, RoHS, ISO 9001,ISO 13485, IATF 16949 |
IPC Standard | IPC 6012 |
Factors Affecting BT PCB's Performance
Several factors influence the performance of a BT PCBs, like materials, production process and design significantly influence BT PCB's performance.
Material Factors
The performance of BT PCB can vary based on material component. The characteristics of the BT resin like its purity level, molecular weight and cross linking density play a role in determining the thermal, mechanical and electrical properties of the PCB. Moreover reinforcement materials such as the type, quantity, and distribution of glass fibers impact the strength, stiffness, thermal expansion of the PCB. Additionally, thickness, purity and adhesion of copper foil also affect the electrical conductivity and reliability.
Factors Influencing BT PCB Manufacturing
The performance of BT PCB is influenced by production process. The lamination procedure, encompassing the pressure, temperature and duration affects the bonding between the resin and copper foil, which in turn impacts the overall strength of the PCB. Drilling and plating precision and quality determine the PCB's dimensional accuracy and reliability.
Design Factors
The width and spacing of copper traces impact signal integrity, impedance control, and heat dissipation. The layer stack-up, which includes the arrangement of copper and dielectric layers, affects signal propagation, crosstalk, and power integrity. Component placement determines signal path length, impedance matching, and thermal management. Effective thermal management, through the design of heat sinks and vias, is crucial for dissipating heat and preventing thermal stress. Together, these elements ensure the overall functionality and reliability of BT PCBs.
BT PCB vs ABF PCB
ABF (Ajinomoto Build-up Film) PCB is made of ABF substrate, which are a type of IC substrate, serves as an intermediary product between IC semiconductor and PCB. ABF substrates are an epoxy-based resin system, currently dominated by the renowned Ajinomoto company.
Acting as a bridge between the chip and the circuit board, ABF ensures the protection of circuit integrity and facilitate efficient heat dissipation. ABF substrates are an epoxy-based resin system, often filled with inorganic materials. They are mainly used as a thinner build-up layer material in high-density interconnect (HDI) PCB. These substrates enable ultra fine line width and spacing, making them suitable for very high-density designs like CPU, GPU, and FPGA, where high-density interconnects are essential.
Feature | BT PCB | ABF PCB |
Material Composition | Bismaleimide-Triazine (BT) resin | Ajinomoto Build-up Film (ABF), epoxy-based |
Thermal Properties | High Tg, good heat resistance | Moderate Tg, less heat resistant than BT |
Electrical Properties | Low Dk and low Df | Low Dk |
Moisture Resistance | Excellent | Good |
Mechanical Strength | Good mechanical strength and stability | Flexible, capable of fine patterning |
Layer structure | Used for core layers | Thinner build-up layers on top of a core |
Application Areas | Mobile phones and memory modules | flip-chip ball grid array, chip-scale packages, high-performance computing and graphics processing units |
Cost | Expensive | Cost-effective |
Why Choose ApplePCB?
Are you in need of an skilled collaborator to produce your high quality BT PCB? You can count on ApplePCB as your go to BT PCB supplier, for state of the art BT circuit board solutions.
Rich Experience
We take pride in our expertise accumulated over a decade in BT-epoxy PCB prototype. Our proficiency in handling the BT resin and its accurate curing process guarantees exceptional performance.
Various Certifications
Our PCB meets UL standards for safety, comply with RoHS to ensure environmental responsibility, and adhere to ISO 9001 for consistent quality management. Moreover we are ISO 13485 certified for medical devices and IATF 16949 certified for automotive industry.
Renowned BT Substrate Suppliers
As a BT PCB manufacturer, ApplePCB maintains strong partnerships with renowned BT substrate suppliers such as Mitsubishi Gas Chemical and Isola, ensuring the highest quality materials in manufacturing process, resulting in robust BT PCB.