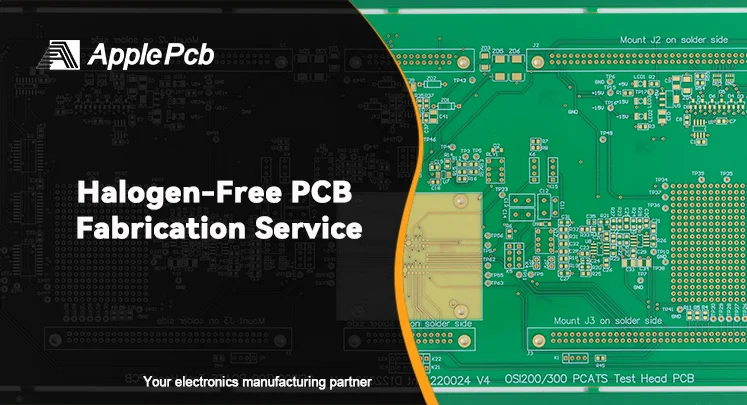
There have been worries about the materials in electronic devices could harm the environment and peoples health in recent years. In the 2000s new rules like the RoHS directive were put in place to restrict the use of dangerous substances like halogenated compounds in electrical products. Because of these regulations electronics sector started looking into options for making PCBs that don't contain halogens.
Understanding Halogen-Free PCBs
PCB made without halogenated substances, known as halogen free PCB, are safer for both the environment and human health. This PCB reduces toxic gas emissions during manufacturing and in fire, which found in consumer electronics, automotive systems, and industrial equipment where environmental regulation and health standard are strict, it also offers improved performance in terms of thermal stability and electrical insulation, making them a preferred choice for high-reliability applications.
What Is Halogen?
Halogens are a set of elements found on the periodic table, usually mean F (fluorine), Cl (chlorine), Br (bromine), I (iodine). The traditional flame retardants based on halogens like polybrominated biphenyls (PBB) and polybrominated diphenyl ethers (PBDE) were utilized to reduce the fire spread in case of PCB overheating. Now, these substances were banned in the electronics. However, bromine flame retardants are still employed in halogen-containing PCBs, with the flame retardant typically being brominated epoxy resin.
Why Are Halogen-Free PCBs Invented?
While halogenated flame retardants were a cost effect solution for fire safety, but they were discovered to release harmful gases when ignited, which not only posed health dangers, such as cancer causing effects but also had negative consequences on the environment.
In the late 20th century, both the European Union and China have prohibited the utilization of PBB and PBDE in electronics, they stipulated moving towards halogen free PCBs, which means substituting old halogenated flame retardants like PBB and PBDE with safer options, like phosphorus or phosphorus nitrogen compounds. Driven by environmental regulations and the growing demand for sustainable electronics, the development of halogen-free PCBs gained momentum.
How Does Halogen-Free PCB Work to Stop Fire?
The core substrate of halogen-free PCB use special epoxy resins made with phosphorus, nitrogen, or other safe alternatives.
Phosphorus-Based Flame Retardants
Phosphorus based compounds form a carbon layer on the PCB surface when exposed to fire, it acts as a barrier, reduces the emission of gas and slow the combustion process.
Nitrogen-Based Flame Retardants
When heated, nitrogen based flame retardants decompose, releasing gases that create bubbles in the char layer, forming a more effective, foamed (intumescent) char for superior heat insulation and flame spread reduction.
Metal Hydroxide Flame Retardants
When metal hydroxides heated, like aluminum hydroxide (ATH) and magnesium hydroxide (MDH) undergo decomposition releasing water vapor. This process absorbs heat decreases the temperature and lowers the chances of ignition.
Materials Used in Halogen-Free PCBs
Common Halogen-Free Materials
Traditionally, materials such as Polybrominated biphenyls (PBB) and Polybrominated diphenyl ethers (PBDE) were used, to make PCB for their flame retardant properties. But those chemicals turned out to be toxic for the environment and people's health. Now, halogen-free PCBs use materials that do not contain halogens:
Category | Material |
Flame Retardants | Phosphorus |
Nitrogen | |
Phosphorus & Nitrogen Compounds | |
Aluminum Hydroxide, Magnesium Hydroxide, Ceramics | |
Resins | Benzoxazine Resins, Bismaleimide Triazine, Tetrafunctional Epoxy Resins, Bisphenol Epoxy Vinyl Esters, Cyanate Esters, Polyimide |
Benefits of These Materials
Environmental Benefits:
Halogen-free PCB are recognized for their minimal environmental impact during production, use, and disposal. Because they ditch those nasty halogenated flame retardants that can be super toxic, thus no harmful fumes or yucky stuff getting released.
Better Insulation:
Halogen free PCBs commonly employ flame retardants that rely on phosphorus or nitrogen compounds. These substances generally exhibit lower polarity when compared to halogens. Moreover certain halogen free resins possess lower polarity, contributing to enhanced insulation resistance.
Thermal Stability:
Halogen free PCBs typically exhibit a higher glass transition temperature (TG) and a lower coefficient of expansion (CTE). As a result they are capable of enduring elevated temperatures, without distortion guaranteeing that the boards retain their integrity and operational effectiveness when subjected to thermal stress.
Comply with Regulatory Standards:
Halogen free PCBs comply with regulations like WEEE and RoHS providing an eco friendly choice for electronics. Back in 2006, electronics relied on flame retardants containing halogens (chlorine and bromine) to slow down fires. But the tide started turning with the introduction of RoHS regulations. These rules said "no way" to two specific halogenated flame retardants in PCB laminates FR4 or CEM 3: Polybrominated biphenyls (PBB) and Polybrominated diphenyl ethers (PBDE). And RoHS got even stricter in 2008 by banning two more harmful chemicals: Tetrabromobisphenol A (TBBPA) and Hexabromocyclododecane (HBCD or HBCDD).
Lower Water Absorption:
The flame retardants halogen free PCBs use, like phosphorus and nitrogen stuff, don't bond with water molecules as easily. So, these halogen-free boards are way better at resisting moisture, making them perfect for humid situation. But it's important to note:these findings may not apply to all halogen-free laminates. The specific water absorption characteristics depend on the exact materials and manufacturing processes used.
Health and Safety Benefits:
The health and safety benefits of halogen free PCBs are substantial, these PCBs do not release harmful halogen acids or other toxic gases when exposed to high temperatures, workers in manufacturing and end-users have fewer health risks, such as respiratory issue, skin and eye irritation, and acidic corrosion.
Market Access:
More than 20% of industries are currently looking for halogen free products, presenting a significant market chance.
Premium Pricing Potential:
More and more consumers are showing a growing concern for the environment. Survey suggest that 68% of them are willing to spend 20% premium on products that are eco friendly.
Towards a Greener Future with ApplePCB
By using material without halogen, ApplePCB not only complies with strict environmental rules but also appeals to environmentally conscious customer. Join ApplePCB and be part of the movement towards a greener future.
Check Our Halogen-free Laminates and Prepregs
Halogen free laminates tend to cost more than laminates containing halogen because they use special flame retardants and involve an intricate manufacturing process. Typically halogen free laminates can be around 10-20% pricier, than halogenated laminates.
Brand | Model |
Rogers Corporation | RO4835™ & RO4360G2™ |
ITEQ | IT-180A |
KB (Kingboard Laminates) | KF Series (KF-611, KF-615) |
Shengyi Technology | S1000H S1165 S1155 Series |
Dupont | Pyralux® TK Series, Kapton |
Panasonic, Isola, Park/Nelco | halogen-free prepregs in various formulations (epoxy, polyimide, etc.) |
Check Our Manufacturing Capabilities
Feature | Capability |
Quality Grade | Standard IPC 2 |
Number of Layers | 1 - 40 layers |
Order Quantity | 1pc - 10000+pcs |
Build Time | 2 days - 4 weeks |
Board Size | Min 6*6mm | Max 457*610mm |
Board Thickness | 0.4mm - 6.5mm |
Copper Weight (Finished) | 0.5oz - 3.0oz |
Min Tracing/Spacing | 3mil/3mil |
Solder Mask Color | Green, White, Blue, Black, Red, Yellow |
Silkscreen Color | White, Black, Yellow |
Surface Finish | HASL (Hot Air Solder Leveling) |
Lead Free HASL | |
Immersion Gold/ENIG (Electroless Nickle) | |
Immersion Silver | |
Immersion Tin | |
OSP (Organic Solderability Preservatives) | |
Min Annular Ring | 4mil |
Min Drilling Hole Diameter | 6mil |
Other Techniques | Gold fingers |
Blind/Buried Vias |
Differences between Traditional PCB and Halogen-Free PCB
Halogen free PCBs provide an option promoting safety and adherence to current environmental regulations. Meanwhile traditional halogenated PCBs continue to be budget friendly and demonstrate relatively good electrical performance.
Halogen-Free PCB
Composition:
Traditionally, flame retardants used in PCBs relied on bromine or chlorine, halogenated elements posing environmental and health risks. In response, a shift emerged towards replacing these with phosphorus or nitrogen-based flame retardants. This evolution led to the development of halogen-free PCBs, crafted from specially formulated epoxy resins that completely exclude halogenated compounds.
Characteristics:
Halogen-free PCBs prioritize environmental safety. Eschewing toxic halogens, they prevent harmful emissions during combustion, adhering to strict regulations like RoHS and WEEE. Furthermore, these materials boast commendable thermal stability for high-temperature applications while maintaining electrical performance comparable to traditional PCBs. However, it's worth noting that the use of halogen-free materials and specialized processes does incur a higher cost.
Soldering:
Halogen-free PCB often coincide with lead-free assembly processes. Lead-free solders typically require higher reflow soldering temperatures of 20°C (36°F) compared to traditional lead-based solders.
Traditional (Halogenated) PCB
Composition:
Halogenated PCBs predominantly feature FR-4 epoxy resin containing brominated flame retardants.
Characteristics:
Thanks to brominated compounds' affordability and impressive flame resistance, initially made halogenated PCBs popular. However, their environmental impact proved severe. Burning these materials releases toxic substances, posing a serious threat to both human health and the environment.
Soldering:
Halogenated PCBs can be soldered at lower temperatures than halogen-free PCBs due to the lower melting points of halogenated materials.
Precautions for Manufacturing of Halogen-Free PCBs
The production of halogen-free PCB presents several unique challenge that different from traditional PCB.
Lamination
Halogen-free PCBs exhibit unique properties, necessitate adjustments to temperature, pressure, and time during lamination. This is because halogen-free materials that require a tailored approach to achieve optimal resin flow and ensure strong bonding between layers.
Drilling
Higher toughness and Tg values in halogen-free PCBs necessitate adaptation of the drilling process. Careful control of speed, feed rate, and coolant becomes crucial to prevent hole wall quality issues. It requires a 5-10% increase in rotation speed and a 10-15% decrease in feed and retract speeds compared to standard parameters.
Cleaning
Halogen-free PCB materials generally have poorer alkali resistance compared to standard FR-4. To prevent white spots on the substrate, avoid prolonged immersion in alkaline stripping solutions. For example, a halogen-free PCB required re-cleaning after solder masking and curing. When cleaned using the standard FR-4 method (immersing in 10% NaOH at 75°C for 40 minutes), white spots appeared. Reducing the immersion time to 15-20 minutes resolved the issue.
Challenges in Adopting Halogen-Free PCBs
Manufacturing Challenges
Halogen free alternatives unlike the PBB and PBDE, are not as readily available, leading to limited choices for suppliers. Additionally, the increased rigidity of these materials can potentially reduce the lifespan of drills by up to 25%.
Cost Implications
Switching to halogen free PCBs can result in increased manufacturing expenses. The materials utilized in halogen free PCBs are generally pricier compared to their halogen containing equivalents, partly because of the economies of scale in conventional PCB production. Finding the substitute materials that adhere to the necessary standards may incur additional costs, also manufacturing adjustments need to be made to incorporate these new materials will drive up the overall cost.
Signal Integrity
Halogen free materials possess unique dielectric that can impact signal stability leading to increased signal loss and impedance mismatches.
Thermal management
These halogen-free materials may showcase different thermal conductivity feature that can influence heat dissipation and the overall thermal efficiency of the PCB.
Prototype Halogen-Free PCB Price and Delivery
The price of Prototype Halogen-Free PCBs and their delivery can vary depending on factors such as the size of the board and the quantity. To help with providing a quote we advise customers to provide us with Gerber files that detail their needs clearly.
As a halogen free PCB factory, ApplePCB generally ships FR4, flexible and aluminum PCBs in 4 to 5 business days. Prototype halogen free PCBs require time for production due to their intricate manufacturing process usually taking around 10 12 working days to finish. Nonetheless we value meeting our customers urgent needs and provide expedited ordering options that can be processed within a week for delivery when necessary.
Why Choose ApplePCB?
Premium Halogen-Free PCBs Manufacturer
ApplePCB specializes in top-tier halogen free PCB production and assembly, adhering to IPC-A-610 Class 3 standards. Our comprehensive offerings include ceramic PCBs, aluminum PCBs, copper substrate PCBs, and halogen-free FR4 PCBs, all designed for cost-effectiveness. We provide a wide range of PCB solutions, including flexible, rigid-flex, and RF microwave PCBs, ensuring a fully halogen-free and RoHS-compliant one-stop service.
Material Selection from Leading Brands
We are a professional halogen free PCB fabricator, offering top-of-the-line halogen-free laminates from Rogers, KB, Shengyi Technology, Corporation, ITEQ, and Dupont. ApplePCB finds the perfect material for your application, whether you need high reliability, thermal performance, high-frequency PCB, halogen free multilayer PCB, or flexible PCB.
Expert Guidance
Our experienced team is available to assist you in exploring the materials that're without halogen. We have an understanding for each use case enabling us to steer you toward the most suitable option.