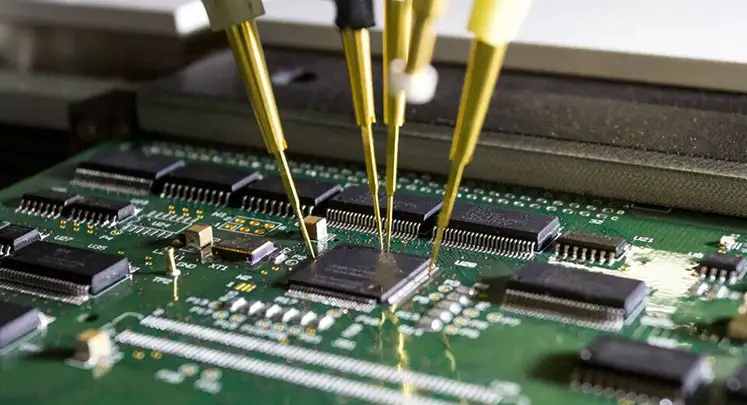
The electronics manufacturing industry is continually evolving. As the complexity of products increases and the demand for higher quality grows, it becomes more important to test and verify product quality. The In-Circuit Test (ICT) emerges as a pivotal element in securing both product quality and reliability.
ICT serves as a testing method that assesses and confirms the functionality of individual components on a printed circuit board assembly (PCBA). Its primary goal is to identify defects or malfunctions at the component level, preventing these issues from advancing to system-level failures.
Our PCB assembly services include ICT testing, an essential step that helps save your business significant time and money by preventing errors from impacting your production.
What is In-Circuit Testing (ICT)?
It's important to have assurance that the electronic components and connections on PCBs function correctly – and this information is needed early in the production process. This is where ICT delivers.
ICT uses specialized equipment with probes to interact directly with your PCBs, measuring parameters like resistance, capacitance, and inductance. It detects shorts and verifies the accuracy of component installation and connections, identifying manufacturing and assembly errors.
While ICT excels at catching these errors, it doesn't diagnose the internal function of individual components. For a comprehensive assessment, you can combine ICT with other testing methods, such as functional or system testing. The ability of ICT testers to examine multiple points simultaneously makes them valuable assets in modern electronics manufacturing.
Understanding the Essentials of Your ICT System
To understand how ICT works, you need to consider the core components of the system and how they function together.
An ICT system typically includes:
● Test system: This system generates signals and takes measurements during testing.
● Test fixture: This specialized fixture holds the PCB and makes contact with its test points.
● Test software: This software controls the test sequences, analyzes results, and generates reports.
Let's look closer at the test system. It contains:
● Test head: Houses the electronics for signal generation and measurement.
● Interface board: Routes signals between the test head and the PCB.
● Control software: Manages test sequences and analyzes results.
● Power supply: Provides power to the PCB under test.
● User interface: Allows an operator to control the system.
● Self-diagnostics: Ensure the accuracy of the testing process.
● Guarding and switching systems: Isolate PCB components during testing.
● Data tools: Collect and report data for quality control and process improvement.
The test fixture is also critical to the ICT process. You'll often encounter a type called a bed-of-nails (BoN) fixture. Here's how it works:
● Purpose: A BoN fixture makes electrical contact with the test points on your assembled PCB. This contact enables the system to measure electrical characteristics, including continuity, resistance, capacitance, and inductance.
● Construction: A BoN fixture is a rigid, flat plate (often aluminum) with spring-loaded pins or probes (the "nails"). These probes align with the test points on your PCB for reliable contact. Each fixture is typically custom-designed for a specific PCB assembly.
● Operation: You place the PCBA into the fixture, and the test system actuates the fixture to initiate testing.
What Defects Does ICT Identify?
ICT helps you identify a range of potential defects on your PCB assemblies, including:
● Circuit Continuity: You can rely on ICT to detect both open circuits, where breaks occur in the electrical path, and short circuits, where unintended connections form between conductive paths.
● Component Values: ICT verifies that components like resistors and capacitors have the correct values according to your design specifications.
● Component Orientation: Diodes, transistors, and other directional components must be placed correctly. ICT checks for orientation errors that could lead to malfunctions.
● Soldering Quality: Before soldering issues affect your product's performance, ICT can identify weak connections from inadequate soldering or shorts caused by excessive solder.
● Missing Components: Even a single missing part can prevent an entire device from functioning. ICT confirms that all components are present on the PCB assembly.
Advantages of ICT
ICT provides a highly accurate and repeatable testing method. Beyond simply ensuring quality and reliability, ICT offers a number of valuable benefits for your PCB production:
● Time and Cost Savings: ICT tests all components on a PCB very quickly – often in just a few minutes or less – making it a significantly faster option compared to other methods. This speed translates into reduced testing costs and a more efficient workflow.
● High-Volume Testing: The efficiency of ICT makes it well-suited for testing large quantities of PCBs. While ICT focuses on individual component testing, it still provides comprehensive insight into the overall functionality of your boards, allowing you to maintain quality standards even in high-volume production environments.
● Customization and Adaptability: ICT systems offer a high degree of customization. You can tailor your hardware and software to match the specific design of each PCB you test. This ensures you're using the most appropriate test parameters for every product. Additionally, you can easily update your testing standards and procedures through software updates.
Disadvantages of ICT
While ICT offers numerous advantages, you should be aware of certain challenges to determine if it aligns with your specific needs and products.
● Upfront Costs and Cycle Time: ICT requires customized programming and configuration of hardware and software for each unique PCB design. This customization involves creating contact points for every component and programming the software with your product's testing specifications. Consequently, you may face higher upfront costs and longer development lead times compared to some other testing methods.
● Individual Testing: ICT excels at testing the functionality of individual components, but it provides limited insight into how those components interact within the complete circuit. To assess the overall functionality of your assembled unit, you will need to incorporate additional testing techniques.
ICT in the Broader Test Ecosystem
For a truly robust quality assurance system, you need a coordinated approach that combines ICT with other testing methods. This allows you to leverage the strengths of each technique while gaining a more complete picture of PCB quality and functionality.
● Automated Optical Inspection (AOI): Often implemented before ICT, AOI verifies solder paste application, component placement, and polarity. This early detection of potential issues streamlines the subsequent ICT process.
● X-ray Inspection: When you need to evaluate the quality of solder joints hidden beneath components (like Ball Grid Arrays), X-ray inspection provides a solution where ICT cannot.
● Flying Probe Testing: While ICT excels in high-volume production, flying probe testing offers greater flexibility for design verification, prototypes, and smaller production runs.
● Functional Testing: Performed after ICT, functional testing replicates the PCB's intended operating environment. This step ensures your board performs its intended functions and builds upon the component-level validation ICT provides.
● System-Level Testing: As the final stage in a comprehensive testing strategy, system-level testing verifies the overall performance of the fully assembled product after ICT and functional testing are complete.
Choose ApplePCB for PCB In-Circuit Testing
When you choose us for your PCB assembly needs, you gain access to integrated ICT services, providing a seamless transition from prototype to production. Reliable testing requires a trusted manufacturing partner – and ApplePCB delivers.
We offer a range of prototyping and medium to small-scale production services designed to accelerate your testing process. With a focus on transparency and quality, we provide dependable, high-quality prototypes without unexpected costs, giving you full confidence in your next round of PCB testing.