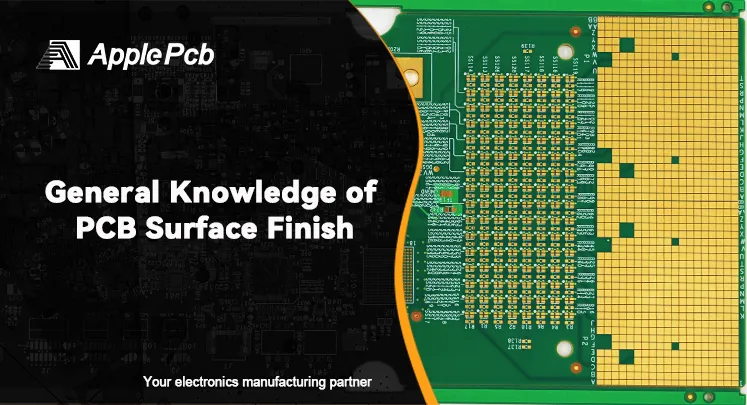
Creating a PCB takes many steps, and the surface finish is a big one.It's how you keep the copper circuits from oxidizing and falling apart and it's also what helps you solder components onto the board.
For a long time, the go-to method was hot air solder leveling (HASL). But as circuits got more complex and environmental regulations tightened, HASL started showing its weaknesses. Newer surface treatments like OSP, ENIG, and ENEPIG have stepped in and become the popular choices.
This guide will walk you through the different types of PCB surface finishes and help you find the perfect fit for your project.
10 PCB Surface Finish Types
Here are 10 typical methods for treating PCB surfaces that each come with their features. ApplePCB will further discuss the advantages and drawbacks of each technique to assist you in determining the solution.
HASL: A Cost-Effective Classic Choice
As we said earlier,HASL (Hot Air Solder Leveling) is a very traditional PCB surface finish method. It form the coating by dipping the board into tin-lead alloy solder and then blowing off the excess solder with a high temperature air knife.
The HASl manufacturing process can be either vertically modesor horizontally modes. And ApplePCB adopts the more advanced horizontal processing, the boards are immersed in solder using nozzlers or rollers positioned at the top and bottom; any surplus solder is then removed by hot air knives. The advantage of the horizontal process is that it balance the gravity differences of the panels and allows for a more uniform HASL coating. Additionally as an in-line process it can be integrated with other processes (such as pre-etching, cleaning and drying) in a single system, which greatly reduces processing time.
The advantage of HASL PCB is that it is less expensive and can be reworked and repaired. Besides the need to expose PCB to temperature of up to 265°C inadvertently add an additional quality check process that can detect possible delamination problems before expensive components are installed.
However, HASL PCB come with several noticeable downsides. The uneven solder coating make them a poor choice for high-density circuits(HDI PCB), fine-pitch layouts, and through-hole components where precise tolerances are essential. Moreover, their high lead content leads to subpar performance in hot and humid conditions, and they do not meet RoHS environmental standards. This has driven the development of a lead-free HASL
Lead-Free HASL: A More Reliable, Greener HASL
Lead-Free HASL is an environmentally friendly surface treatment process that improve on traditional HASL. It use tin copper or tin silver alloys (e.g. 99.3% tin and 0.6% copper) instead of tin-lead alloys to make it RoHS compliant. It doesn't cost much more than HASL, but it has a higher surface finish and is reliable in high temperature, high-humidity environment. However, similar to conventional HASL, the solder coating of Lead-Free HASL can be uneven and is not suitable for high density PCB.
OSP: Eco-Friendly Finish with Excellent Solderability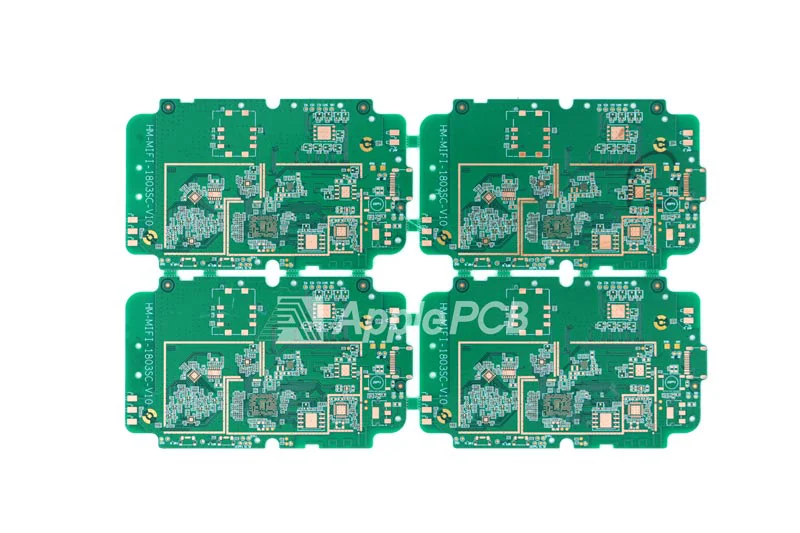
OSP (Organic Solderability Preservative) is an environmentally friendly PCB surface treatment process, which requires micro-etching to enhance the adhesion of copper to the OSP solution. In order to ensure that a smooth and uniform film, we need to maintain the stability of the micro-etching speed, the general ApplePCB will be etching speed control in the range of 1.0 to 1.5 μm per minute.
OSP provides advantages including good solderability and ease of production at a reasonable cost. The water based materials utilized do not contain substances and comply with the RoHS environmental regulations. Nevertheless the surface of OSP is sensitive and susceptible, to damage and scratches potentially affecting its solderability. Additionally its coating is thin and uneven which can make accurate measurement difficult.
Compared to other PCB finish types like ENIG or HASL, OSP has a relatively short shelf life, typically under 12 months. Moreover, OSP PCBs require strict storage condition: a relative humidity of 30-70% RH and a temperature between 15-30℃. When vacuum-packed, release paper should be used to prevent abrasion, along with desiccants and humidity indicator cards to protect against moisture.
ENIG: Premium Finish for High-Reliability Applications
ENIG, also called enig Immersion Gold, actually has two coating. The first layer is a nickel layer(4 - 7 μm thick), which is chemically deposited on the bare copper surface. The nickel layer act as a barrier between the copper and gold layer, preventing the subsequently deposited gold layer from diffusing into the copper. It will also create Ni₃Sn₄ which reacts with tin to improve the solderability and conductivity of the PCB board.
The gold coating shield the nickel coating and minimizes contact resistance. It is available in thicknesses from 0.05 to 0.23 μm. Thinner gold layer reduce cost but provide less corrosion and oxidation resistance; thicker gold layers improve durability but result in increased cost. For most applications, it is best not to exceed a thickness of 0.15 μm, as a thicker layer may result in non-wetting of the solder paste or cracking of the solder.
ENIG plating offers a surface and strong resistance to corrosion which makes it ideal for supporting BGAs and high density SMT components in various industries including aerOSPace and defense sectors. Moreover ENIG PCB finishes are an option for application that involve multiple assembly cycles as the coating can endure repeated rounds of reflow soldering.
ENIG finish is pricier compared to other surface finish because of the inclusion of gold in its composition. Moreover it is not ideal for high temperature settings as the nickel layer might undergo cracking or peeling when subjected to stress which could affect its dependability. It demands a sophisticated manufacturing process due to the nickel layers vulnerability to oxidation and difficult to visually inspecting.
Compared to other finishes, ENIG finishes are more expensive because they contain gold in their composition. Therefore, it is very important to optimize the design to reduce the unnecessary gold immersion area to reduce the cost while meeting the product capability. There are many factors that affect the area of gold immersion. From the design point of view, the more complex the design, usually need to sink gold area is larger, resulting in increased costs. Therefore, when designing PCBs, we can minimize the size of the pads or increase the spacing, and in areas where mechanical stress or electrical capabilities are not required, other surface treatment methods (such as HASL or OSP) can be selected.
On the production side, production equipment, technology and labor costs also affect the price of immersion gold, ApplePCB uses advanced automated equipment, through the optimization of the production process, we can improve production efficiency and reduce the loss of gold, thus reducing the production cost of immersion gold. In addition, ApplePCB's production headquarters is located in China, which reduces our labor and site costs, so we can offer more competitive prices to our customers. You can contact us at the bottom right corner to get a quote.
ENEPIG: The Upgraded Version of ENIG
ENEPIG(Electroless Nickel Electroless Palladium Immersion Gold) is a multilayer metal finishing technique that set it apart from ENIG by incorporating a palladium layer between the nickel and gold layers offering enhanced protection against corrosion, for the nickel layer. Typically, the nickel is between 3 and 6μm and the palladium is about 0.1 to 0.5μm . The gold layer is very thin, about 0.02 to 0.1μm and therefore the palladium layer may be exposed in case of severe mechanical damage or scratch.
The advantage of ENEPIG is that it provide a very flat surface for PCB, which is ideal for plated hole, fine pitch, BGA and small component. As a lead free process, it meet environmental requirement and can accommodate multiple cycle assemblies, which is particularly suitable where repeated soldering is required.
In addition, ENEPIG plating offer higher reliability lead bonding than ENIG, and the addition of a palladium layer between the nickel and gold layers effectively prevents the "black pad" problem (corrosion and oxidation of nickel), greatly improving board reliability with a shelf life of up to 12 months or more. This treatment provides an ideal choice for high reliability applications that require long term stability.
However, ENEPIG has some disadvantages, mainly that it is more expensive, even a little more expensive than ENIG. In addition, the complexity of the process requires extra care during production and handling to ensure the integrity and capability of the coating, which add to the difficulty of manufacturing and the management requirement. However these issue may be an acceptable price to pay for application seeking high reliability and capability.
IAg: Economical with Excellent Solderability
IAg, also known as Immersion Silver, enhances the electrical conductivity and solderability of copper by plating it with a thin layer of silver.Typical thicknesses of IAg range from 4-12u".The IAg process provides a flatter surface than HASL, is easier to use than OSP, and is less expensive than immersion gold. In addition, it is lead-free and RoHs compliant.
However, sinking silver may be subject to loss under certain conditions (e.g. humid and corrosive environments). Therefore it is best to solder within 24h of removal from storage. The storage time of silver-sinking PCBs in a dry environment is usually around 6-12 months, if it exceeds twelve months then a solderability test needs to be carried out before assembly to ensure the reliability of the PCBs.
Immersion Tin: A Finish with Excellent Solder Compatibility
Immersion Tin is a lead-free surface treatment that meet RoHs compliant. It is the deposition of a thin layer of tin on the surface of copper, typically 20-50u"thick. Since the tin layer is usually white in appearance, immersion tin is also known as "white tin". Compared to immersion gold and immersion silver, immersion Tin is less costly. Since all solder is tin-based, the immersion tin finish is basically a perfect match for any type of solder with good solderability and thermal stability. It is also an ideal finish for crimp pin insertion application.
The close connection between tin and copper may cause the development of "tin whisker" which could result short circuit. In this regard, ApplePCB will add certain organic additives to the tin immersion solution, so that the tin layer is a granular structure to avoid problems caused by tin whiskers. Moreover, the thiourea used in the immersion tin process is a known carcinogen and therefore needs to be operated under safe conditions.
In addition, immersion tin has a shorter shelf life and is more susceptible to damage than immersion gold or silver. Therefore immersion tin PCBs need to be assembled within 6-12 months and need to be handled with care. In order to avoid problems during transportation and handling, it is recommended to consolidate the PCB manufacturing and assembly processes at the same location to minimize the risk of possible damage.
Hard Gold Plating: Optimal Choice for High Wear Applications
The primary contrast, between gold and ENIG lies in the fact that hard gold is applied through electroplating than a chemical reaction to create a thicker layer of gold over copper material. Additionally small quantities of valuable metals, like cobalt, nickel or iron are incorporated during the plating process to enhance the durability of the gold coating. These element alter the grain structure of the deposit, resulting in a finer grain structure that makes the coating shinier and more resistant to slippery wear. The hardness of hard gold usually range from 130-200 HK.
Hard gold is commonly chosen for components that need to endure plug in and unplug due to its exceptional resistance to wear and tear—such as in gold finger and contact points where durability is crucial for long lasting stability. Moreover the thicker plating layer of gold offers minimal contact resistance and ensures good electrical conductivity, which is essential, for high frequency applications that rely on signal integrity.
However, the disadvantages of hard gold are obvious. First, it cost more than ENIG because more gold is used in the plating process. If the entire board is plated with gold, then the cost can be very high. Also the non-precious metal elements present in hard gold oxidize at soldering temperature, resulting in a less intact solder joint, making it unsuitable for very sensitive joining application such as thermo ultrasonic or ultrasonic lead bonding.
Soft Gold Plating: Highly Ductile and Corrosion-Resistant Finish
Soft gold is also electroplated to form a layer of gold over a layer of copper, unlike hard gold, soft gold plating does not have any intentionally co-deposited elements. The purity of gold in soft gold plating is 99.9% or better, with very few impurities, usually unintentional carbon (only 10ppm or less). In contrast, hard gold has an elemental purity of 99.0% and impurity levels as high as 2800 ppm.
Because of this extreme purity, soft gold plating exhibit the truly noble properties of gold. It is extremely resistant to corrosion, and if plated to a sufficient thickness, soft gold plating can even be “non-porous”. Its light opacity is also ideal for some medical catheterization devices that require a visible component. Compared to hard gold, it has excellent ductility, lower resistance (three times that of hard gold plating), and produces stronger soldered joints, making it ideal for PCBs that require curved or sensitive connections.
The disadvantages of gold are mainly the lower hardness (typically 20 90 HK25) and therefore scratching and abrasion, which is not well suited to applications requiring frequent insertion and removal. In addition, the grain structure of soft gold plating is not as fine as that of hard gold plating and therefore does not have the glossy appearance of hard gold from the outside. Soft gold plating is usually more expensive than gold plating due to the very high purity requirements throughout the production process.
Mixed Surface Finishes
Mixed finishes refer to more than two finishes on a single PCB. Depending on the requirements, we can choose different combinations, ApplePCB can offer you ENIG+OSP, HASL+plating hard Gold, ENIG+plating hard Gold, plating gold+plating hard Gold, OSP+plating hard Gold and other mixed finishes. Gold, plating gold+plating hard Gold, OSP+plating hard Gold, etc. You can contact us in the lower right corner for detailed inquiries.
How to Choose the Right Surface Finish?
In the face of so many types of surface treatment, how to pick the most suitable surface treatment for your PCB, ApplePCB with 15 years of surface treatment manufacturing experience for you to organize the five key elements to consider.
1. Applicability
In actual application different surface treatment processes are affected by flatness, abrasion resistance, weldability, oxidation resistance and other factors, supporting different applications. applePCB has compiled the following table for you, detailing the applicability of each surface treatment process in different application scenarios.
ENIG | ENEPIG | Hard Gold | Soft Gold | Silver | Tin | |
BGA and μBGA | √ | √ | √ | √ | √ | √ |
Connector | √ | √ | √ | × | × | × |
Fine Pitch SMT | √ | √ | √ | √ | √ | √ |
Flip Chip | √ | √ | √ | √ | √ | √ |
Wire Bonding | √ | √ | × | √ | × | × |
Solder Joint Integrity | Good | Good | Poor | Poor | Excellent | Good |
2.RoHs Standards
If your project needs to comply with environmental standards and you want to reduce hazardous waste. Then it's time to choose a lead-free finish in addition to HASL: LF-HASL, OSP, ENIG, Tin, Silver, Hard Gold, Soft Gold ENEPIG.
3.Cost Considerations
The cost of different finishes actually varies greatly. Of the above finishes HASL , LF-HASL, OSP are the more economical choices for projects with tighter budgets. If you are willing to invest more in higher capability and reliability, consider ENIG or ENEPIG.
4.Storage Life
Storage life is an important consideration as some finishes may undergo oxidation, discoloration or other forms of deterioration due to the passage of time. Of these PCB surface finish types, IAg, OSP and Tin have relatively short storage lifetimes, usually under 12 months. If your printed circuit boards are to be stored for long periods of time or in harsh conditions, ApplePCB recommends that you choose a finish with a longer storage life: ENIG, HASL, Gold and ENEPIG.
ApplePCB's Surface Finishing Process Capabilities
PCB Surface Finish | Production Panel Size: | Thickness | PCB Thickness |
LF HASL/HASL with Lead | Min.size: 150x230mm, Max.size: 520x650mm, | 1-40um | 0.5-3.5mm |
ENIG | Min.size: 150x230mm, Max.size: 520x800mm, | NI:100-200U" AU:1-4U" | 0.2-6.5mm |
Vertical Immersion Tin | Min.size: 60x80mm, Max.size: 500x600mm, | 0.8-6um | 0.3-5.0mm |
Horizontal Immersion Silver | Min.size: 60x80mm, Max.size: one side ≤500mm | 6-12u" | 0.3-5.0mm |
OSP | Min.size: 60x80mm, Max.size: one side ≤500mm | 0.2-0.4um | 0.3-5.0mm |
Plating Hard/Soft Gold | Min.size: 150x230mm, Max.size: 450x500mm | 2-50u" | 0.2-5.0mm |
ENEPIG | Min.size: 150x230mm, Max.size: 520x800mm, | NI:100-200U" AU:1-4U" PD:1-6U" | 0.2-6.5mm |
Plating Lead /Tin(Etching resist) | Lead Content 100PPM |
Conclusion
As you can see, surface finishes need to be chosen carefully and it is not possible to simply conclude that one surface finish is better than another in all cases. The choice should be based on the specific design and purpose of the board, and ApplePCB's team of DFM engineers can perform a professional evaluation of your design needs to help you select the most appropriate surface treatment process and provide you with subsequent PCB fabrication and assembly services.