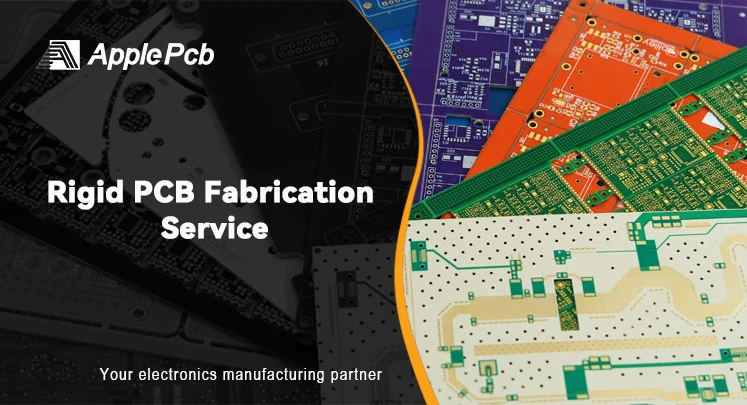
What is a Rigid PCB?
Rigid Printed Circuit Boards serve as the cornerstone of the PCB industry. With a reputation for reliability and longevity, they are widely utilized in computer motherboards and smartphones. These circuit boards can be customized as-sided, double-sided, or multi-layered to meet the intricate demands of electronic devices. Their sturdy nature provides a base for accommodating electronic components encompassing contemporary surface mount devices and traditional through-hole components. Rigid printed circuit boards are suitable for wave soldering, reflow soldering and manual soldering tasks of components. Many engineers are choosing printed circuit boards as their board solution due to their superior stability and longer service life.
The structure of a Rigid PCB
The complete rigid printed circuit boards usually consist of four layers structure; a substrate layer, a copper layer, a solder mask layer, and a silkscreen layer. These layers are firmly bonded together using adhesives and heat. In multilayer rigid PCB, the configuration becomes more intricate with multiple substrate layers and copper layers to meet increased electrical performance needs and intricate circuit layouts.
Substrate Layer
The substrate layer serves as the component of a sturdy printed circuit board primarily responsible, for offering structural support. Depending on the material used laminates can be classified into types.
Material Type | Model | Characteristics |
Phenolic Resin Copper Clad Laminate | FR-1 | Economical, Flame Retardant |
Phenolic Resin Copper Clad Laminate | FR-2 | High Electrical Properties, Flame Retardant (Cold Punch) |
Epoxy Resin Copper Clad Sheet | FR-3 | High Electrical Properties, Flame Retardant |
Glass Cloth Substrate | FR-4 | Standard material for high-performance electronics |
Glass Cloth Substrate | FR-5 (G11) | Heat Resistant |
Glass Cloth Substrate | GPY | Glass Cloth-Polyimide Resin |
Composite Substrates | CEM-1, CEM-2 | CEM-1 Flame Retardant; CEM-2 Non-Flame Retardant |
Composite Substrates | CEM3 | Flame Retardant |
Ceramic Substrates | Aluminum oxide | / |
Ceramic Substrates | Aluminum Nitride (AlN) | / |
Ceramic Substrates | Silicon Carbide (SiC) | / |
Common substrates are glass cloth substrates FR4, aluminum substrates, and ceramic substrates. Each of these three different materials has its characteristics:
1. FR4 substrate: FR4, as one of the most common Laminates, offers balanced electrical properties, high flexibility, and cost-effectiveness for most Rigid PCB manufacturing.
2. Aluminum substrate: as a kind of metal-based copper-clad laminate, the aluminum substrate has good heat dissipation and conductivity. Therefore, they can carry higher currents and are suitable for high-power products. Fragile ceramic substrate compared to the aluminum substrate has higher mechanical strength and can provide good mechanical support for PCB.
3. Ceramic substrate: Ceramic substrates are well known in the field of electronics for their ability to conduct heat ranging from 25W to 230W. This surpasses the heat dissipating abilities of materials such as FR4 or aluminum which typically 3W. The excellent thermal performance guarantees dispersal of heat making them essential, for demanding applications that need effective heat control.
Moreover, the insulating properties of these substrates inherently provide insulation eliminating the necessity, for insulating layers. This feature simplifies the design process. Enhances the end products' efficiency.
Despite their benefits, ceramic substrates are more delicate compared to aluminum and FR-4 posing a risk of breakage during manufacturing. This fragility necessitates manufacturers to utilize production techniques and technology to minimize waste and enhance yield rates.
Copper Layer
The copper layer is the second layer of a rigid PCB and sits on top of the substrate layer. Through adhesive and heat, the copper foil can be firmly pressed onto the substrate for stable data conduction.
Typically copper covers both surfaces of the substrate layer, in printed circuit boards. This allows for connections on both the back sides through, through holes leading to an efficient and space saving circuit layout. However, in budget devices that do not require advanced functionality the substrate layer may have copper on just one side to reduce expenses.
The copper layers thickness differs across boards. Is usually classified as 1oz (35μm) 2oz (70μm) and 3, oz (105μm). This thickness of copper influences the capacity of the PCB to carry signal voltage and current.
Solder Mask
The protective layer, on circuit boards is typically composed of epoxy resin. While green is a common choice for the solder mask there are also colors, like purple, blue and red available. Its primary purpose is to safeguard the copper layer and offer insulation.
·Why do most PCBs use green solder masks?
1. Protection of eyesight: The green color is less irritating to the eyes, which enables production and maintenance personnel to protect their eyes and eliminate fatigue.
2. Lower cost: green ink demands more, the largest shipments, so the purchase cost is also lower.
3. Favorable to AOI: A green background color is more conducive to the recognition effect of the instrument.
Silkscreen layer
The Silkscreen layer is located above the solder mask layer and is the outermost layer of the PCB. It consists of characters such as numbers, letters, logos, etc., and plays the role of marking and positioning. Through accurate marking, we can efficiently and accurately paste and solder components in the surface mount device process, but also conducive to fast and easy maintenance and troubleshooting of the circuit board in the future.
What are the advantages and disadvantages of Rigid PCBs?
Rigid PCBs are circuit boards make from a substrate like fiberglass or composite epoxy. They are commonly employed in electronics equipment, for their outstanding electrical capabilities and longevity. In this section, ApplePCB will explore the advantages and disadvantages uses and other key features of PCBs.
Advantages
Structural Stability
Rigid PCBs are made of a robust substrate material, typically FR4, which provides excellent physical stability. This stability ensures the SMD mounting process and improves the efficiency and quality of PCB assembly.
High Reliability
Rigid PCBs are known for their durability under conditions of temperature and physical stress. This feature helps protect them from damage during movement, set-up, and use, which is why they are suitable for challenging environments such as the industrial and automotive industries.
Easy to Manufacture and SMD
The manufacturing and assembly procedures for rigid printed circuit boards (PCBs) have been thoroughly completed. The flat and non-bendable nature of these PCBs simplifies the component assembly process, resulting in increased efficiency and precision, ultimately increasing production cost-effectiveness.
However, PCB production is generally divided into sample production, mass production and mass production, especially for high-layer PCBs, achieving high-volume production is still a challenge, requiring the adoption of advanced technology and strict quality control measures.
Cost-effective
For simpler single- and double-sided rigid PCBs, design and manufacturing costs are relatively low and the production process is simpler. Better for projects with limited budgets or short turnaround times.
While the upfront cost of design and production may increase for multilayer rigid PCBs, their rugged and reliable nature ultimately makes them a more economical option and can be used for a long time.
Disadvantages
Insufficient Flexibility
Rigid PCBs cannot be bent or folded, which limits their use in certain applications, such as wearables or other products that require a circuit board to bend.
Volume and Mass
Rigid circuit boards are typically thicker and heavier than flexible circuit boards, and may not be suitable for use in electronic devices.
Mechanical Stress Effects
While rigid printed circuit boards are known for their robustness, they are susceptible to strain in certain situations, especially in environments with frequent vibrations or sudden impacts. Constant stress exposure can cause the PCB and its parts to deform or malfunction.
Fix the Difficulty of Modification
Once a rigid PCB has been produced, it can be very challenging and costly to change or repair it, especially when layers of multi-layer PCBs are involved.
There are Different Types of Rigid PCBs Offered by ApplePCB
1. Energy Storage Board
Energy storage panels are commonly used in batteries, electric vehicles, solar energy storage devices, and similar applications. They must be able to withstand high temperatures and effectively manage large currents. This requires the use of materials such as FR 4、thick copper and the implementation of a heat dissipation structure to ensure the stability of the energy storage panel in handling high-current charging and discharging operations in high-temperature environments. In addition, since the energy storage system is expected to have a lifespan, the energy storage panel must be durable. This requires consideration of surface treatment and anti-corrosion measures to maintain service life.
2. Power Strip
The main function is to convert electrical energy into a stable voltage suitable for use. It is widely used in various electrical products, which can be divided into switching power supply PCB, monitoring power supply PCB, high-frequency power supply PCB, LED power supply PCB, and production equipment power supply PCB.
Power boards typically have high efficiency, enabling fast and accurate power control through efficient control algorithms and circuit design.
3. Industrial Control Board
Industrial control boards are mainly used in industrial control systems, GPS navigation, automation equipment, PLC controllers, industrial computers, etc.
The industrial control board generally uses low-power chips, so as to save energy consumption, run for a long time without high temperature problems, and have strong stability. The industrial control board can work in a high temperature environment of up to 90 degrees, and its own heat dissipation control ability is strong, and it can well adapt to the harsh industrial environment of high temperature and dust.
4. Consumer Electronics Boards
Consumer electronics circuit boards play an important role in devices such as smartphones, tablets, and home appliances. To meet the demand for compact consumer electronics, these boards are designed to be density, integration, thinness, and light weight. To achieve this, PCB manufacturers employ high-precision drilling and screen printing techniques to ensure that lightweight design requirements are met without compromising the accuracy and reliability of circuit connections.
How to Find a Reliable PCB Manufacturer?
Number of layers
The production cost of rigid PCBs increases with the number of layers. In addition, the higher the number of layers, the more the design and manufacturing process requires the manufacturer's greater expertise.
Laminated Material
The choice of material used to manufacture a PCB has a significant impact on its functionality and overall quality. Therefore, when producing PCBs, it is crucial to choose a brand of production materials. SOME OF THE POPULAR BRANDS IN THE MARKET INCLUDE KB, ROGERS, AND ITEQ, AMONG OTHERS.
Manufacturing Technology
When choosing a PCB manufacturer, it's crucial to evaluate their ability to handle the process, as design and manufacturing needs vary from application to application. For example, to manufacture HDI boards, manufacturers must be adept at laser drilling and microvia technology. For high-power applications, manufacturers need to have expertise in producing thick copper plates, for example.
Test
The final stage of checking the performance of a PCB is testing. Manufacturers need to meticulously test rigid PCBs using a variety of manual and automated methods to guarantee their performance and quality.
ApplePCB’s Key Manufacturing Capabilities
Item | Process Capability |
Layer Count | 1-36 Layers |
Board Thickness | 0.2-8mm, Tolerance ±5% |
Maximum PCB Size | 500x1500mm |
Material Type | FR-4, PTFE, ROGERS, ARLON, etc. |
Copper Thickness | Range from 1/2 oz to 20 oz |
Advanced Drilling | Machine Drill: 0.15mm-6.4mm |
Laser Drill: 0.075mm-0.2mm | |
Surface Finishing | HASL, LF HASL, ENIG, Immersion Tin/Silver/Gold, OSP, ETC. |
Warp | Conventional: 0.75%;Limit:0.5%;Max:2.0%. |
Impedance Control | ±7% |
Testing Methods | AOI |
Flying Probe | |
In-Circuit | |
X-Ray Inspection | |
Functional Testing | |
Certifications | IATF 16949:2016 |
ISO 9001:2015 | |
ISO 14001:2015 | |
ISO 13485:2016 | |
UL |
Why Choose Rigid PCB for ApplePCB?
1. Fast and Efficient Production
ApplePCB offers fast lead times for rigid PCB manufacturing. We can achieve this with our quick turnaround services:
layer | 2 | 4 | 6 | 8 | 10 |
The fastest | 24 hours | 48 hours | 72 hours | 72 hours | 3 days |
Normal time | 4 days | 6-7 days | 7-8 days | 8-10 days | 10-12 days |
produce | 8-10 days | 10-12 days | 11-13 days | 13-16 days | 13-16 days |
2. Advanced Rigid PCB Technology
With more than 15 years of rich PCB manufacturing experience, ApplePCB has mastered a variety of complex rigid PCB manufacturing technologies, including:
● In-pad via rigid circuit board
● Embedded copper rigid PCB
● Back drill rigid PCB
● Deep groove rigid PCB
● Countersink rigid PCB
● Blind and buried rigid PCB
3. Excellent Service Experience
Our team is dedicated and caring, committed to providing top-notch service to ensure that your orders are processed in a timely and accurate manner. We pride ourselves on our track record of 100% customer satisfaction and zero complaints, which exemplifies our commitment to excellence and customer care.
4. Reliable Delivery Guarantee
We understand that your deadline is important to you. As a result, ApplePCB is committed to delivering every order on time and ensuring that the PCB arrives in perfect condition.
When choosing an ApplePCB, it's not a question of choosing a PCB provider, but choosing a collaborator who can enhance your project.